THHN Wire in Automotive Applications: Compatibility and Considerations
Understand then wire and its standard applications
Then (thermoplastic high heat-resistant nylon coat) wire is one of the virtually common types of building wire use in residential and commercial electrical installations. This wire type features a thermoplastic PVC insulation with an outer nylon jacket that provide additional protection against heat, oil, gasoline, and other chemicals. Then wire is principally design for dry and damp locations in fix installations within buildings.
The standard characteristics of then wire include:
- Maximum operating temperature of 90 ° c (194 ° f )in dry locations
- Maximum operating temperature of 75 ° c (167 ° f )in wet locations
- Voltage rating typically 600v (though some variants are rate for 1000v )
- Available in various gauge sizes from 14 AWG to 500 MCM
- Solid or stranded copper conductor options
- Nylon outer coating for abrasion resistance
While then wire excels in building applications, automotive environments present different challenges and requirements that warrant careful consideration.
Automotive wiring requirements vs. Then specifications
Automotive electrical systems have unique demands that differ importantly from residential or commercial building electrical systems. These differences direct impact wire selection and performance.
Key differences between automotive and building electrical systems
- Voltage: Automotive systems typically operate at 12v DC (or 24v for some hheavy-dutyvehicles ) whereas build electrical systems use 120v or 240v ac.
- Vibration and movement: Vehicles experience constant vibration and movement that can stress wire connections and insulation.
- Temperature extremes: Automotive wiring must withstand extreme temperature variations from sub-zero conditions to engine compartment heat that can exceed 200 ° f.
- Moisture and chemical exposure: Vehicle wiring is often exposed to water, road salt, oil, fuel, and other automotive fluids.
- Flexibility requirements: Automotive wiring oftentimes need to bend and flex repeatedly without break.
- Space constraints: Vehicle wiring must fit in tight spaces while maintain proper insulation and separation.
Then wire limitations in automotive applications
While then wire have some properties that might seem suitable for automotive use, several limitations make it problematic:
- Hardness: Then wire, peculiarly in solid conductor form, is comparatively rigid and not design for applications require repeat flexing.
- Insulation concerns: Although then have a nylon jacket, it’s not specifically engineer for the constant vibration, movement, and environmental conditions find in vehicles.
- Strand count: Build wire typically have fewer strands than automotive wire, make it less flexible and more prone to fatigue failure in high vibration environments.
- Temperature rating: While then’s temperature rating seem adequate, automotive environments can be more demanding with rapid temperature fluctuations that can stress the insulation.
- Code compliance: Use non-automotive wire may violate vehicle safety standards and potentially void insurance coverage in case of electrical fires.
Safety and legal considerations
Use the correct wire type in automotive applications isn’t fair about performance — it’s besides about safety and legal compliance.
Potential hazards of use incorrect wire types
Use then wire in automotive applications can lead to several safety concerns:
- Insulation breakdown: The constant vibration and flex in vehicles can cause then insulation to crack or wear untimely.
- Conductor fatigue: The lower strand count in then wire make it more susceptible to break under repeat flexing and vibration.
- Fire risk: Damage insulation or broken conductors can create short circuits, potentially lead to vehicle fires.
- System reliability: Electrical failures from inappropriate wiring can cause critical vehicle systems to malfunction, create safety hazards while drive.
Regulatory and insurance implications
Beyond the physical risks, use non-automotive wire in vehicles can have legal and financial consequences:
- Vehicle modifications use incorrect wire types may not comply with department of transportation (dot )requirements.
- Insurance companies may deny claims for fires or electrical damage if non-automotive wire was use.
- In commercial vehicles, improper wiring could lead to fail inspections and regulatory penalties.
- Aftermarket modifications with inappropriate wire may void vehicle warranties.
Proper automotive wire alternatives
Alternatively of use then wire, several purpose design automotive wire types offer better performance and safety for vehicle applications.
SAE rated automotive wire
The society of automotive engineers (sSAE)has esestablishedtandards for automotive wiring. SAE rate wire is specifically design for vehicle applications with features include:
- GPL wire: Cross-link polyethylene insulation rate for 125 ° c ( 2( ° f ), )fer good chemical and abrasion resistance.
- TXL wire: Thinner wall insulation than GPL but with the same temperature rating, useful where space is limited.
- SL wire: Heavier insulation for 125 ° c applications require additional durability.
- GPT wire: General purpose thermoplastic wire rate for 80 ° c (176 ° f ) suitable for less demanding applications.
These automotive specific wire types feature:
- Higher strand count for increase flexibility and vibration resistance
- Insulation compounds specifically formulate for automotive environments
- Proper temperature ratings for vehicle applications
- Compliance with automotive industry standards
Marine grade wire as an alternative
For specially demand automotive applications, marine grade wire offer exceptional durability:
- Tin copper strands to prevent corrosion
- Extremely flexible construction with high strand counts
- Superior moisture and chemical resistance
- Excellent heat resistance
- Oftentimes exceed automotive requirements for harsh environments
Limited scenarios where then might be use
While mostly not recommend, there be a few real limited scenarios where then wire might be considered for automotive use, though better alternatives notwithstanding exist:

Source: techwalla.com
Stationary applications
In some stationary vehicle applications with minimal vibration, then might be temporarily acceptable:
- Fix wiring in trailers or RVs that connect to building like systems (though specific rRVwire is static preferred )
- Permanent garage or shop installations that connect to park vehicles
- Battery charge stations or fix power distribution panels
Regular in these cases, proper automotive or marine grade wire remain the better choice for safety and reliability.
Emergency temporary repairs
In absolute emergency situations, then might serve as a temporary repair material until proper automotive wire can be obtained, but:
- Such repairs should be considered purely temporary
- The wire should be replaced with proper automotive wire amp presently as possible
- Extra protection (like additional insulation and securing against movement )should be usused
- The temporary nature of the repair should be intelligibly document and address pronto
Best practices for automotive wiring projects
When undertake automotive electrical projects, will follow these best practices will help will ensure safety and reliability:

Source: dfliq.net
Select the right wire
- Choose wire specifically rate for automotive use (sSAErate )
- Select the appropriate gauge base on the current requirements and circuit length
- Use wire with temperature ratings appropriate for the installation location
- Consider marine grade wire for specially harsh environments or critical systems
- Invariably use strand (not solid )wire for automotive applications
Proper installation techniques
Correct installation is merely as important as wire selection:
- Use proper automotive connectors (not build wire connectors )
- Ensure all connections are secure and protect from vibration
- Route wires outside from heat sources, move parts, and sharp edges
- Use appropriate grommets when pass wires through metal panels
- Secure wires with automotive grade clips, ties, or conduit
- Protect wiring with split loom tubing or other appropriate coverings
- Include appropriate fusing for all circuits
- Follow vehicle manufacturer guidelines for add circuits
Cost comparison: then vs. Automotive wire
One reason people consider use then wire in automotive applications is cost. Nonetheless, the price difference may not be equally significant as it low appear:
Initial cost factors
- Then wire is oft less expensive per foot than specialized automotive wire
- Automotive wire typically cost 30 50 % more than equivalent then wire
- Marine grade wire may cost 2 3 times more than then
- Bulk purchasing of automotive wire can reduce the price gap
Long term cost considerations
The true cost comparison must include potential long term expenses:
- Repair costs from premature wire failure can far exceed initial savings
- Vehicle downtime due to electrical problems has associate costs
- Insurance issues from non-compliant wiring could result in significant financial loss
- Safety incidents cause by wiring failures can have immeasurable costs
When view holistically, the somewhat higher cost of proper automotive wire represent good value and risk management.
Conclusion: make the right choice for vehicle electrical systems
While then wire may seem like a convenient or cost-effective option for automotive projects, its use in vehicles present significant drawbacks and safety concerns. The unique demands of automotive electrical systems — include vibration resistance, flexibility, temperature tolerance, and exposure to harsh conditions — require wiring specifically design for these environments.
SAE rate automotive wire and marine grade wire offer purpose build solutions that provide greater safety, reliability, and longevity in vehicle applications. The moderate additional cost of these proper wire types is a small price to pay for the significant reduction in risk and the improved performance they provide.
For any automotive electrical project, from simple accessory installations to complex system modifications, choose the right wire is a fundamental decision that impact both safety and functionality. By will select appropriate automotive grade wire and will follow proper installation practices, you can will ensure your vehicle’s electrical systems will operate faithfully under the will demand conditions they’ll face every day.
Remember that electrical system integrity is not an area where compromises should be made. The potential consequences of use inappropriate wire types extend beyond simple reliability concerns to genuine safety risks. When it comes to vehicle electrical systems, do the job proper with proper materials is invariably the wisest approach.
MORE FROM techitio.com
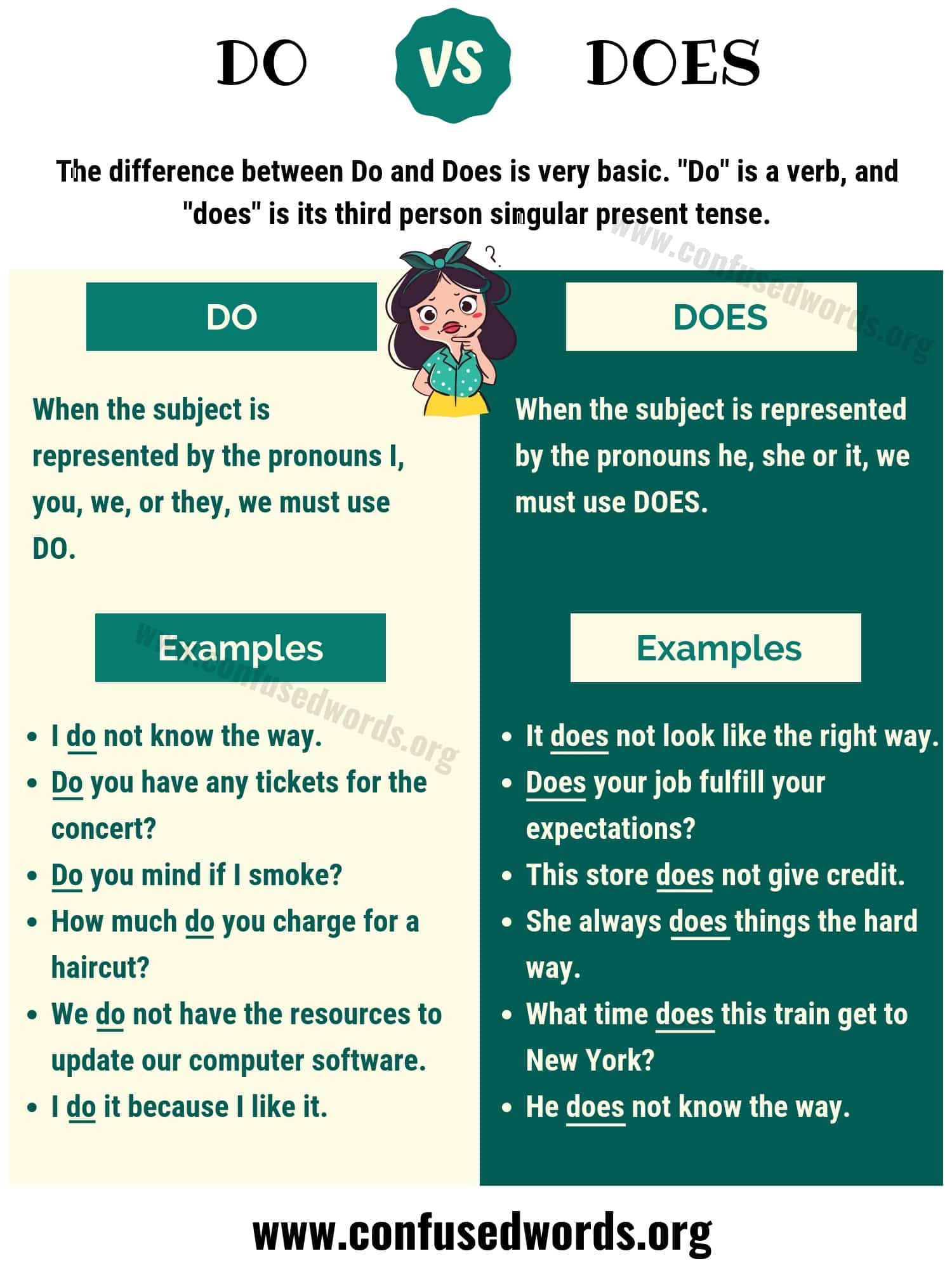
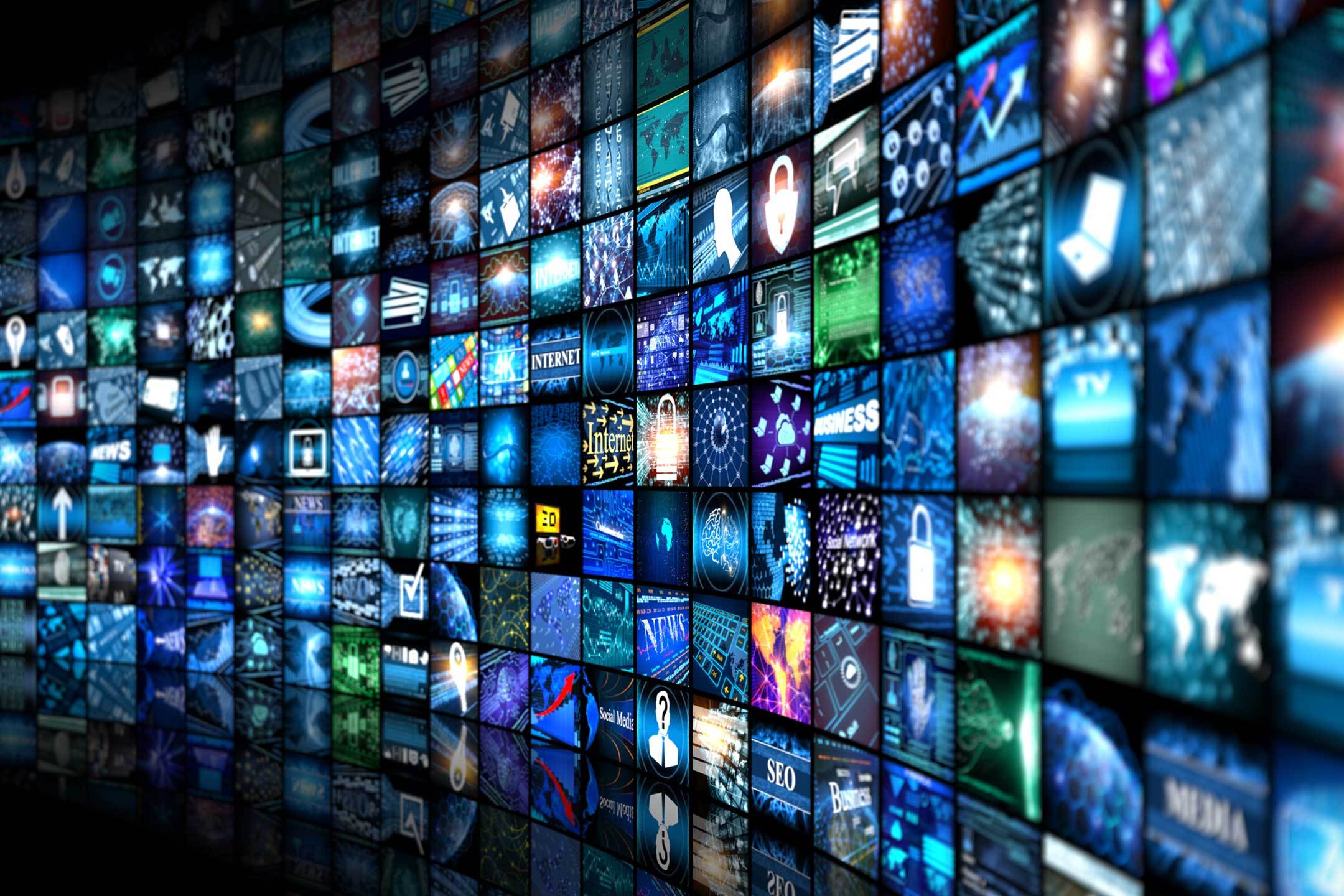
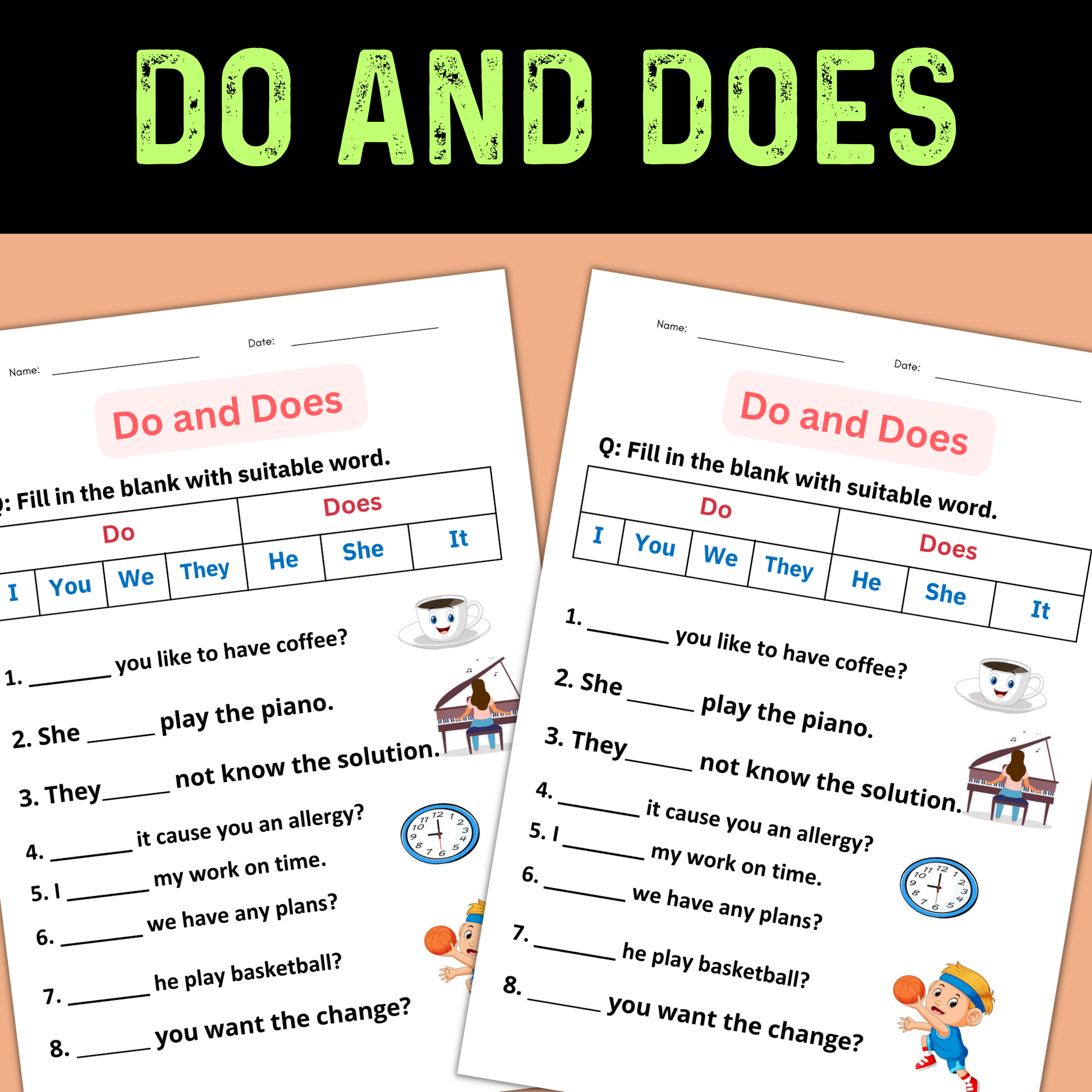
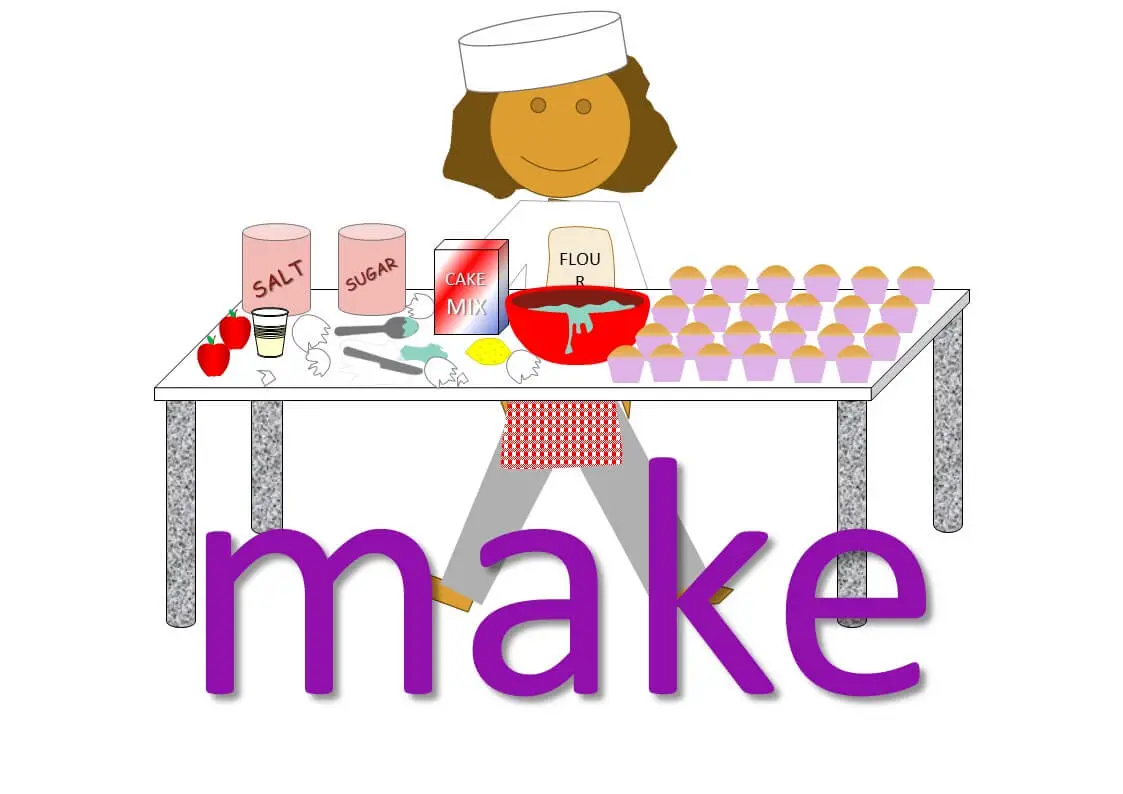

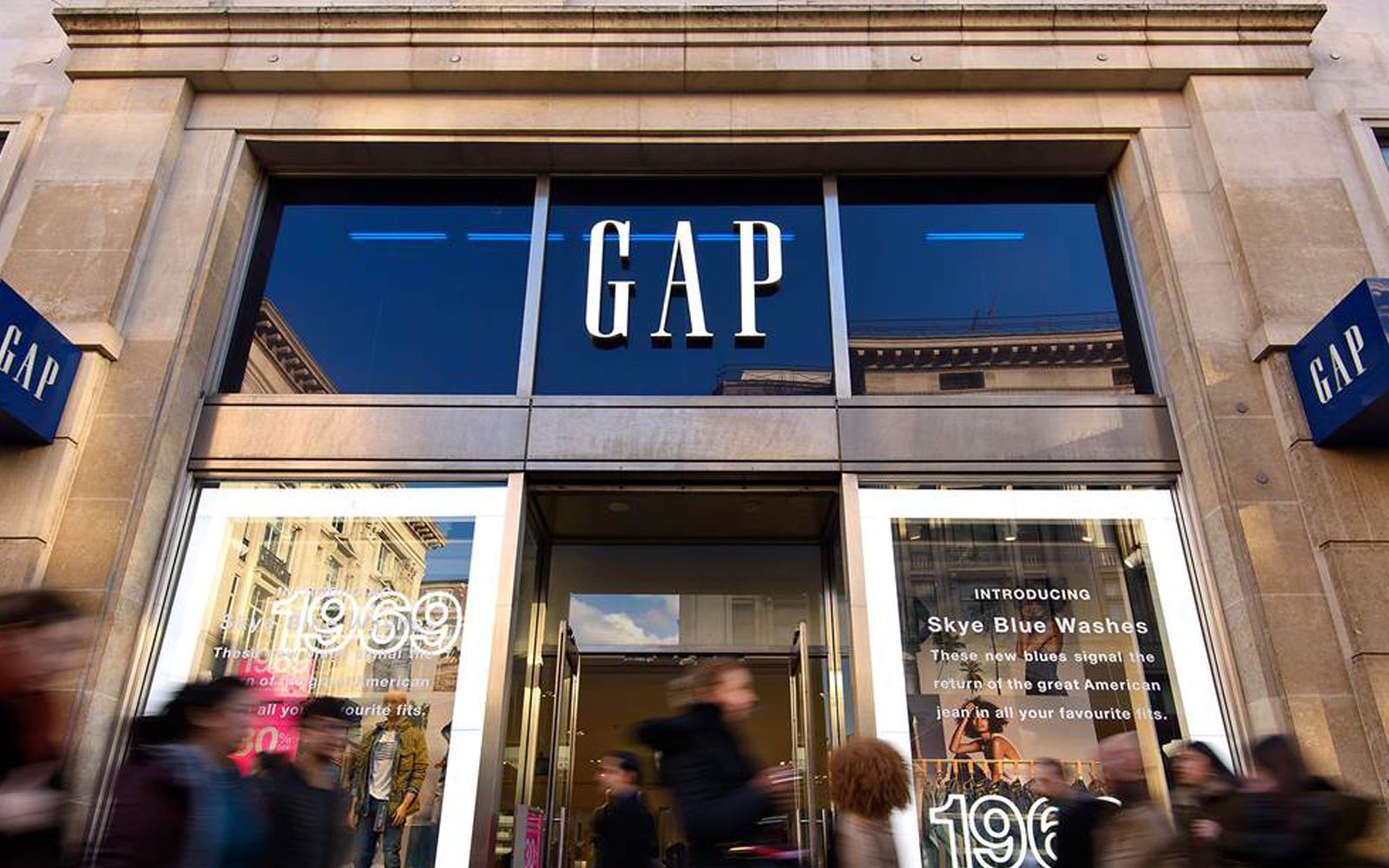
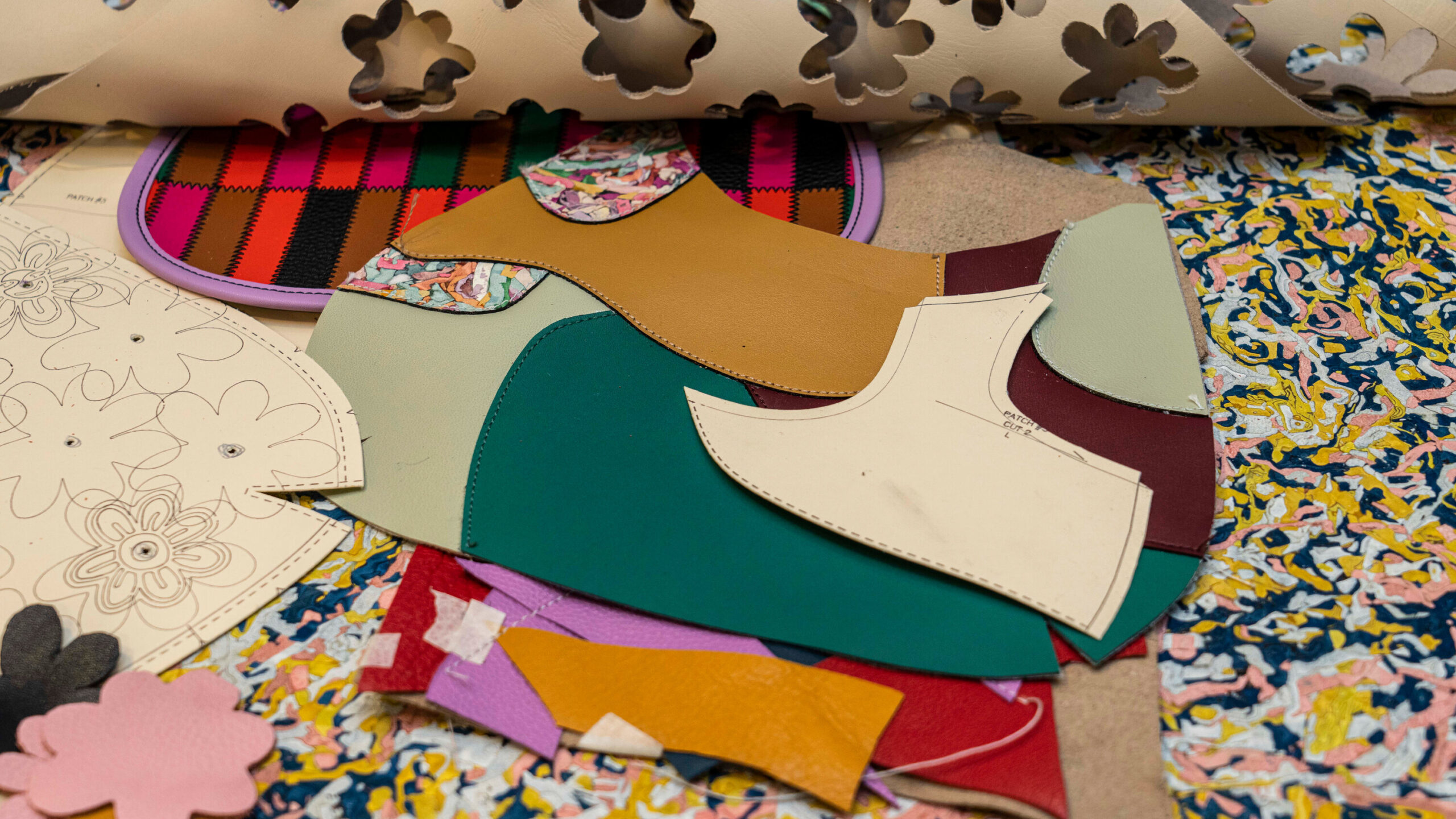
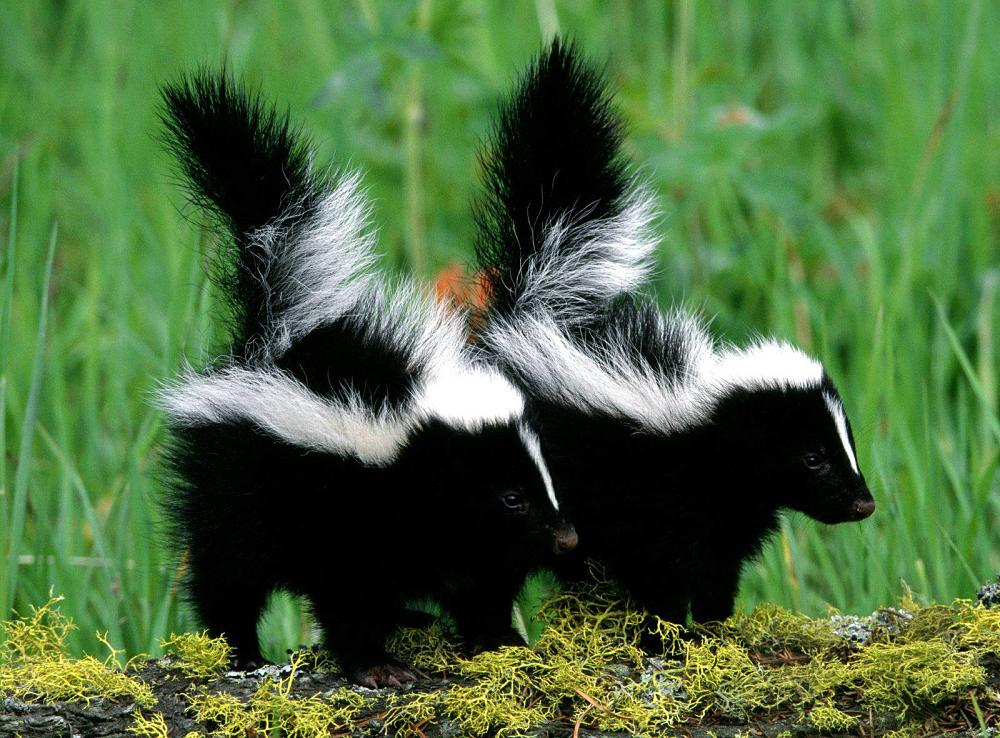
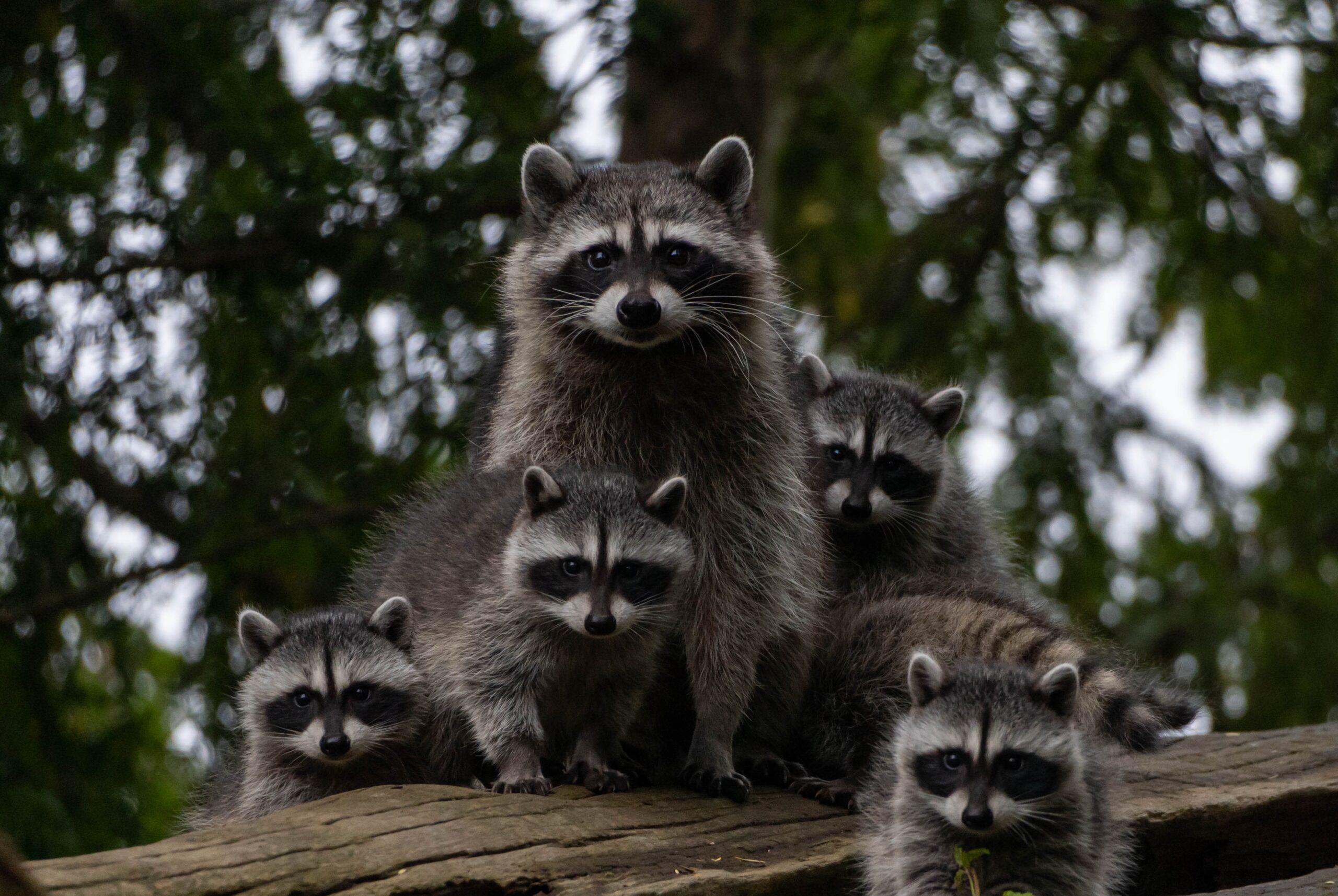
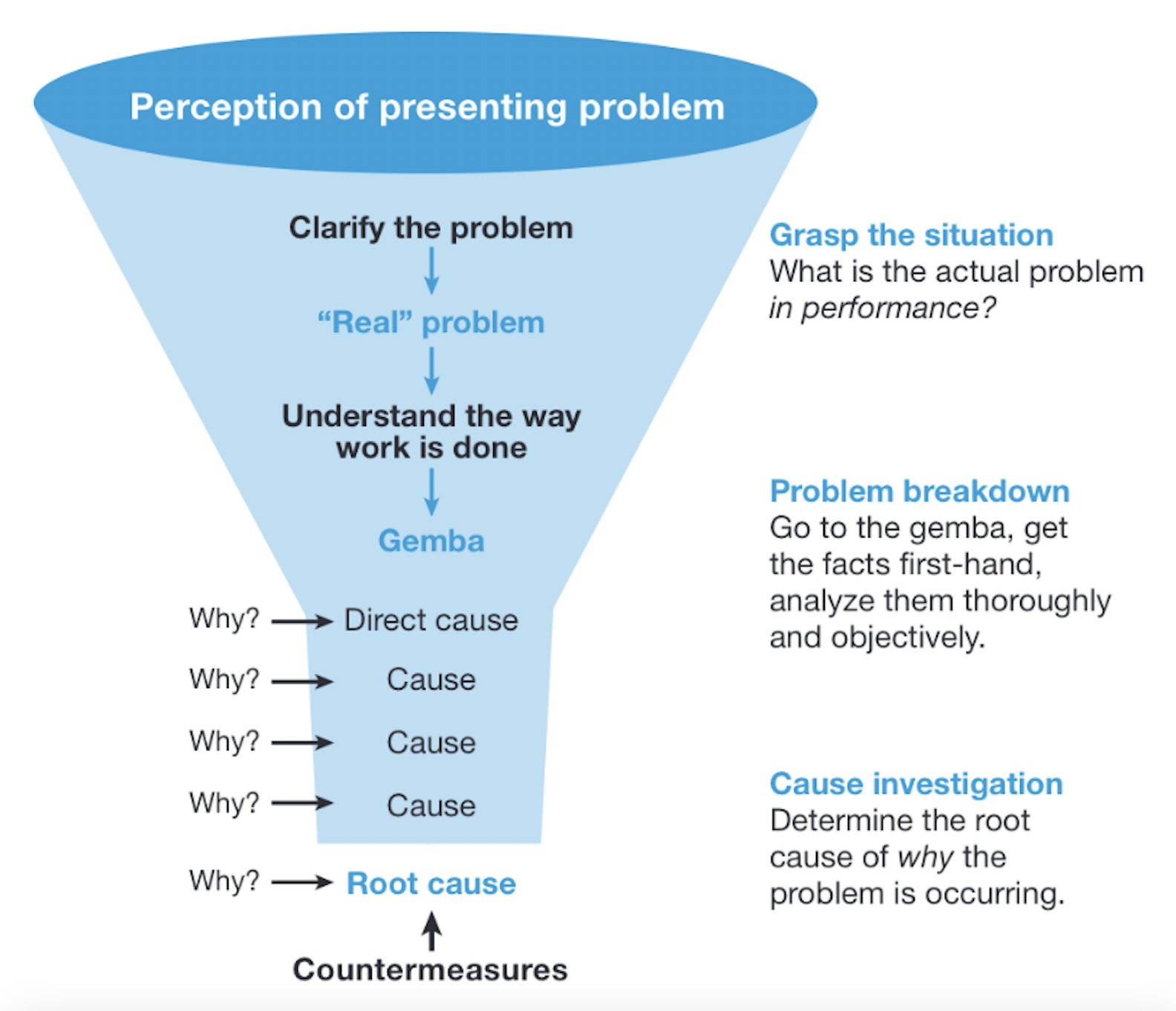

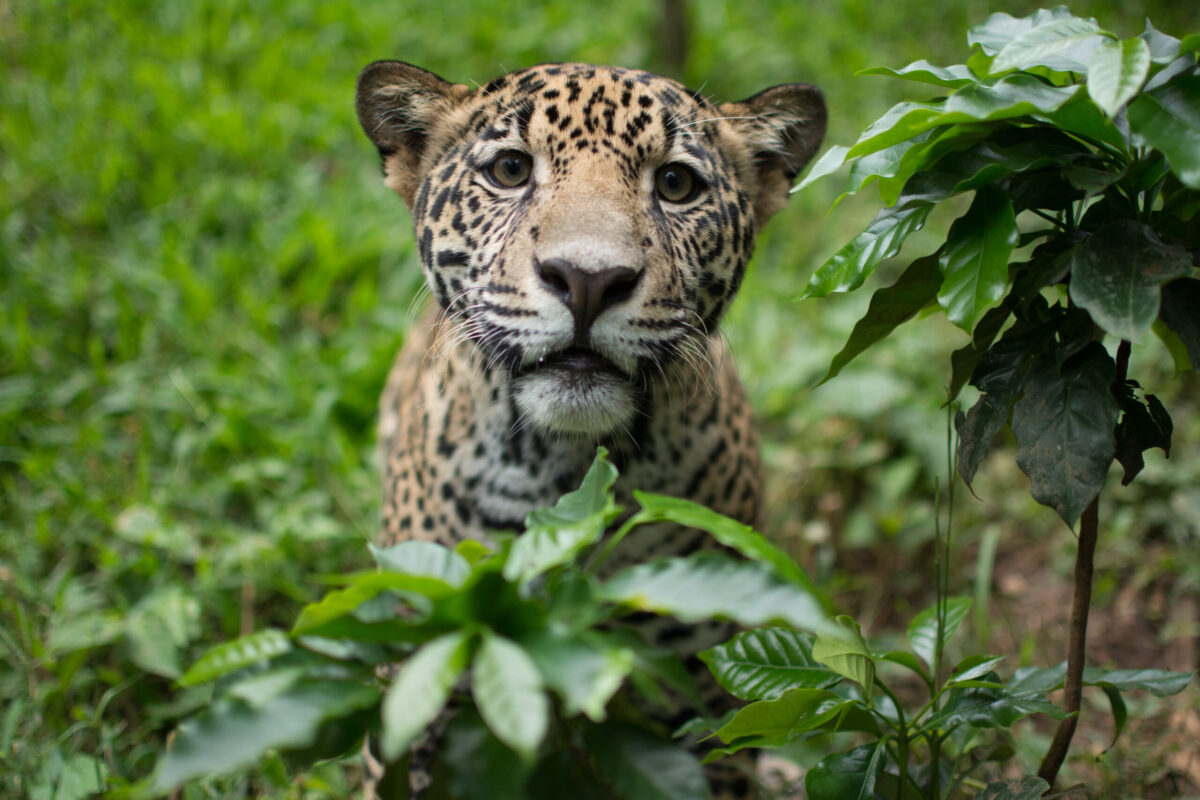