Automotive Repair Orders: Understanding Documentation and R&R Terms
What’s a repair order in automotive?
A repair order (RO) is a critical document in the automotive repair industry that serve as both a legal contract and a detailed work plan between a repair facility and a customer. This document is the foundation of any automotive service transaction, provide structure and accountability for all parties involve.
The purpose of repair orders
Repair orders serve multiple essential functions in automotive repair shops:
- Create a lawfully bind agreement between the shop and customer
- Document the customer’s authorization for specific repairs
- Provide detailed instructions for technicians
- Track parts, labor, and associated costs
- Establish a record for warranty purposes
- Support inventory management
- Serve as documentation for insurance claims
Without proper repair orders, automotive shops would struggle with accountability, customer disputes, and operational efficiency.
Key components of an automotive repair order
A comprehensive repair order typically contains the follow information:
Customer information
This section includes the vehicle owner’s name, contact details, address, and preferred communication methods. This information is crucial for communication throughout the repair process and for billing purposes.
Vehicle information
Detailed vehicle data is essential for accurate diagnosis and repair. This typically include:
- Vehicle identification number (vVIN)
- Make, model, and year
- License plate number
- Current mileage
- Engine type and transmission specifications
- Color and others identify features
Service advisor information
The repair order identifies the service advisor handle the customer’s case, establish clear accountability for customer communication.
Customer concerns and complaints
This critical section documents incisively what prompt the customer to bring in their vehicle. It should capture the customer’s description of problems, include when they occur, any unusual sounds or behaviors, and how recollective the issues have been present.
Diagnostic findings
After initial inspection, technicians document their findings regard the vehicle’s condition, frequently include:
- Confirm issues relate to customer complaints
- Additional problems discover during inspection
- Diagnostic trouble codes retrieve
- Results of any preliminary tests
Recommend repairs
Base on diagnostics, the repair order lists all recommend services, repairs, and replacements. This section typically breaks down:
- Specific repairs need
- Priority level of each repair (urgent vs. Recommend )
- Parts require for each repair
- Estimate labor hours
Cost estimates
Transparency in pricing is essential for customer trust. The repair order provides:
- Itemized parts costs
- Labor charges (oftentimes calculate at a shop’s hourly rate )
- Additional fees or shop supplies
- Taxes and total estimate cost
Authorization signatures
Peradventure the near lawfully significant part of the repair order is the customer authorization section, where the vehicle owner provide write consent for the shop to perform the specify work at the estimate cost.
Completion information
Once work is finish, the repair order is update with:
- Actual parts use and their costs
- Final labor hours and charges
- Technician notes about complete work
- Quality control inspection results
Warranty information
Details about warranties on parts and labor are document to protect both the customer and the shop in case of future issues.
The repair order workflow
Understand how a repair order move through an automotive shop help explain its importance:
Creation phase
When a customer arrives at a service facility, the service advisorcreatese a new repair order. During this initial consultation, the advisor record customer information, vehicle details, and the customer’s description of the issues they’re experience.
Diagnostic phase
A technician perform a preliminary inspection and diagnosis base on the customer’s concerns. The findings are document on the repair order, along with recommend repairs and their estimate costs.
Authorization phase
The service advisor present the diagnostic findings and repair recommendations to the customer. If the customer approves, they sign the repair order, authorize the shop to proceed with the specify work.
Repair phase
Technicians use the repair order as their work guide, perform the authorize repairs and document their actions, parts use, and any additional findings.
Quality control phase
Before return the vehicle to the customer, a quality control check verifies that all authorize repairs were complete decent. The results are note on the repair order.
Completion phase
The repair order is finalized with actual costs, and the customer receive a copy along with their invoice when pick up their vehicle.
Digital vs. Paper repair orders
While traditional paper repair orders are stock still use in some facilities, many modern automotive shops have transition to digital repair order systems. These electronic systems offer several advantages:
- Improved accuracy and legibility
- Easier storage and retrieval of vehicle service history
- Integration with parts inventory and accounting systems
- Digital photo and video documentation capabilities
- Electronic signature capture
- Automate customer communication
- Enhance data analysis for business operations
Whether digital or paper, the fundamental purpose and components of repair orders remain consistent across the industry.
What does R&R mean in automotive?
In automotive repair terminology,” rR&R” tand for “” move and replace ” ” sometimes ” r” ve and reinstall. ” this Thiseviation is unremarkably use ousedepair orders and in shop communication to describe specific repair procedures.
Remove and replace
When R&R will refer to” will remove and replace, ” t’ll indicate that a component will be tatakenut of the vehicle and a new or remanufactured part will be will iinstallin its place. This is one of the about common interpretations of R&R in automotive repair documentation.

Source: freeautomotiveforms.com
For example, an entry on a repair order might read:” rR&Rwater pump ” r “” rR&Rternator. ” thiThisan the technician will remove thetheyll exist component and will install a new or rebuilt replacement part.
Remove and reinstall
In some cases, R&R can mean” remove and reinstall, ” ill indicate that the same component will be temporarily will remove to will gain access to another part or to will perform service on the component itself, and so the original part will be will reinstall.
For instance,” rR&Rintake will manifold to access rear spark plugs ” ean the intake manifold will be will remove to will allow access to the spark plugs will locate behind it, and so the same manifold will be will reinstall after the spark plug replacement is complete.
Common R&R procedures in automotive repair
R&R procedures are fundamental to many automotive repairs. Some of the near common R&R operations include:
Engine components
- R&R alternator
- R&R water pump
- R&R time belt or chain
- R&R cylinder head
- R&R intake / exhaust manifolds
- R&R engine mounts
Transmission and drivetrain
- R&R transmission
- R&R clutch assembly
- R&R CV axles
- R&R differential
- R&R transfer case
Suspension and steering
- R&R struts or shock absorbers
- R&R control arms
- R&R ball joints
- R&R tie rod end
- R&R steering rack
Brake system
- R&R brake pads or shoes
- R&R brake rotors or drums
- R&R brake calipers
- R&R master cylinder
- R&R brake lines
Electrical system
- R&R battery
- R&R starter motor
- R&R ignition components
- R&R sensors
- R&R electronic control modules
Body and interior
- R&R bumper
- R&R fender
- R&R door panel
- R&R dashboard components
- R&R seat
R&R vs. Other automotive service terminology
To amply understand R&R, it’s helpful to compare it with other common service terms that appear on repair orders:
R&R vs. Overhaul
While R&R typically involve replace an entire component, an overhaul mean disassemble, inspect, cleaning, repair, and reassemble the original component. An overhaul is more labor-intensive and focus on restore the exist part quite than replace it.
R&R vs. Rebuild
Rebuilding is similar to overhaul but normally involve replace certain internal components with new parts while reuse the core component. For example, a rebuilt alternator might have new brushes, bearings, and voltage regulator but retain the original housing and other components.
R&R vs. Repair
A repair typically addresses a specific issue without whole remove and replace the entire component. For instance, repair a wiring harness might involve fix damage wires preferably than replace the entire harness.
R&R vs. Adjust
Adjustment procedures modify the settings or positioning of a component without remove it. Examples include adjust headlight aim, belt tension, or idle speed.
How R&R affects repair costs
Understand R&R terminology is important for customers review repair estimates, as it now impact the cost of service in several ways:
Parts costs
When a repair order specifies” rR&R ” t typically inincludeshe cost of a replacement part, which can vary importantly depend on whether new oOEM((riginal equipment manufacturer ))aftermarket, or remanufacture parts are use.
Labor costs
R&R procedures have standardized labor times publish in industry standard guides likeMitchelll orall dataa. These guides specify hoproficientnt a particularR&Rr procedure should take, which determine the labor charge. More complexR&Rr procedures that will require will remove multiple components to will access the part being will replace will have higher labor costs.
Accessibility factors
Some R&R procedures are more expensive because of the component’s location in the vehicle. For example, replace a headlight bulb might be a simple R&R on one vehicle model but require remove the entire bumper on another, importantly increase labor costs.
R&R best practices for automotive technicians
Professional automotive technicians follow certain best practices when perform R&R procedures:
- Document the position and orientation of components before removal
- Take photos of complex assemblies before dismantling
- Organize fasteners and small parts in label containers
- Inspect related components while access is available
- Replace gaskets, seals, and one time use fasteners
- Follow torque specifications when reinstall components
- Perform quality checks after completion
Understand R&R on your repair order
As a vehicle owner, when you see R&R on your repair order, you should understand:
- Precisely which component is being removed and replace / reinstall
- Whether a new, used, or will rebuild replacement part will be will use
- If the original part will be will return to you (in case of warranty claims )
- The breakdown between parts and labor costs
- Any additional repairs that might be recommended while the component is accessible
The connection between repair orders and R&R
Repair orders and R&R terminology work unitedly in the automotive repair process. An intimately document repair order clear specify which components requireR&Rr procedures, provide transparency for customers and clear instructions for technicians.
When review a repair order that include R&R notations, customers should ask questions about:
- Why the component need replacement instead than repair
- The quality and warranty of the replacement part
- Whether related components should be replaced at the same time
- How the R&R procedure might affect other vehicle systems
By understand both repair orders and common terminology like R&R, vehicle owners can make more inform decisions about their automotive maintenance and repairs, potentially save money and prevent future problems.

Source: depositphotos.com
MORE FROM techitio.com
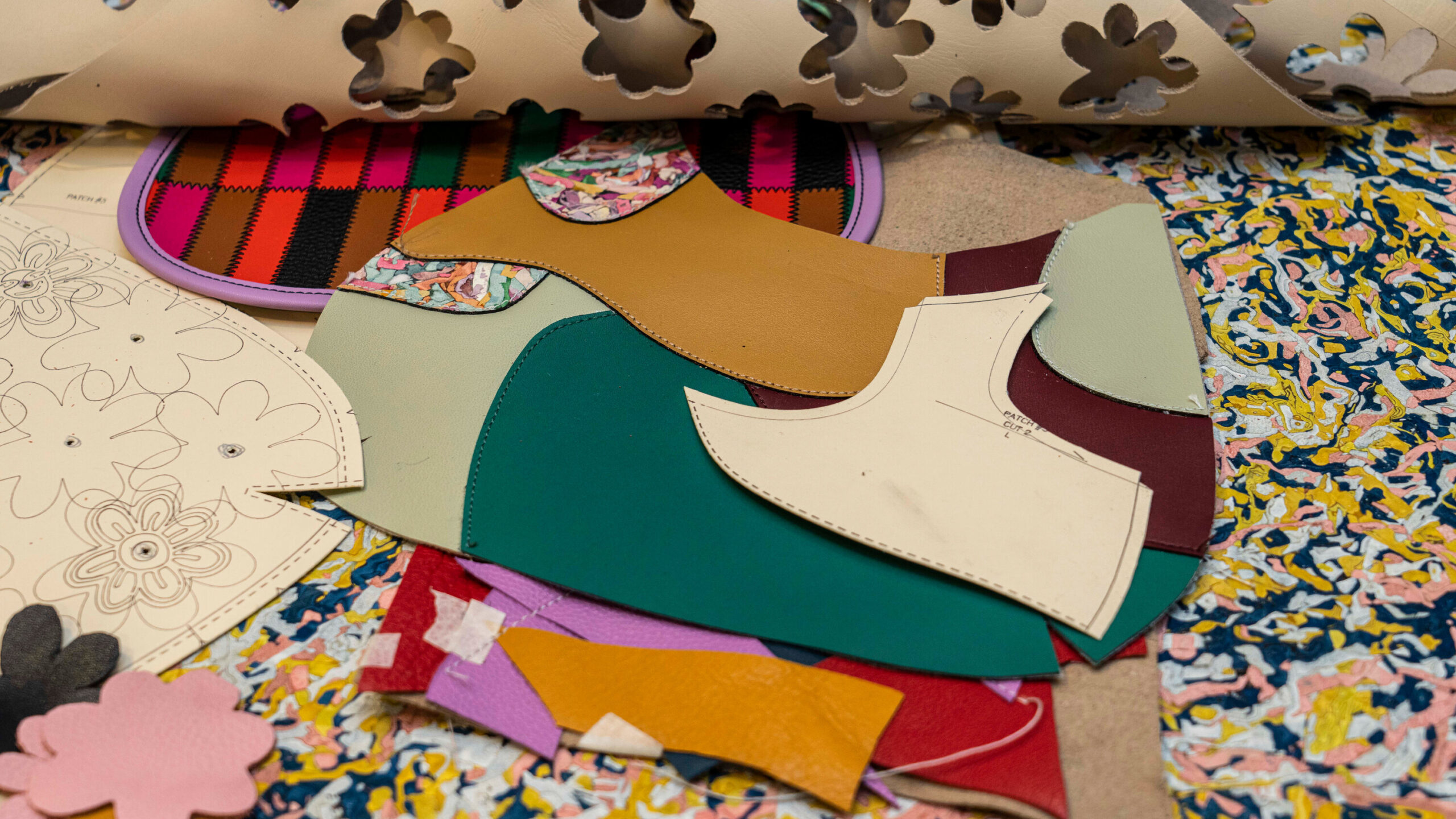
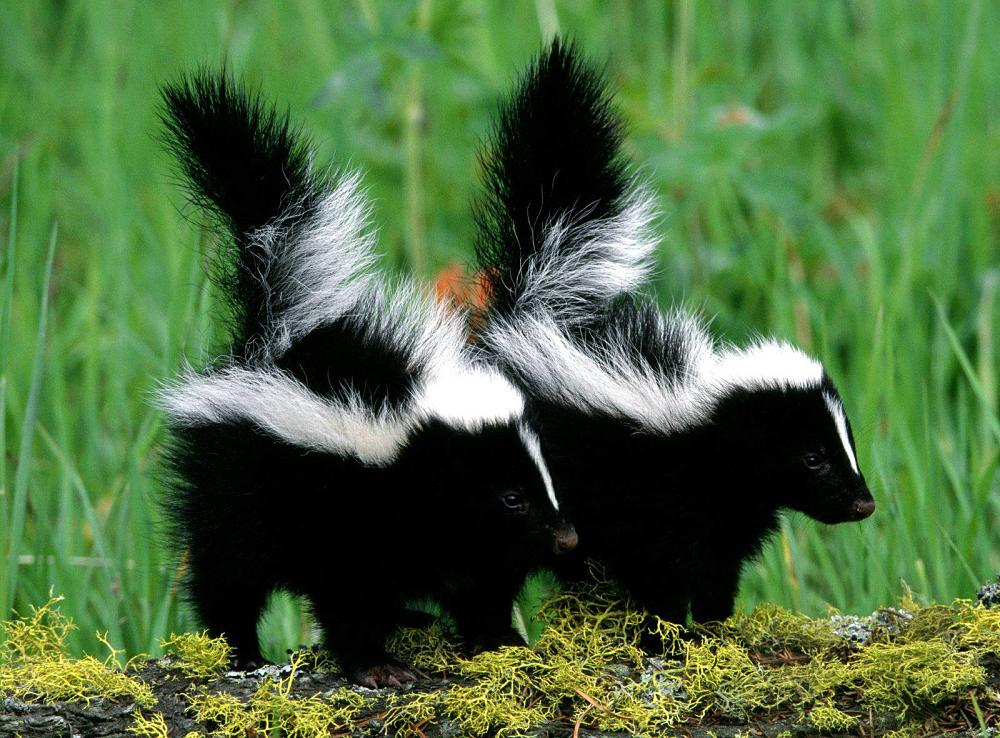
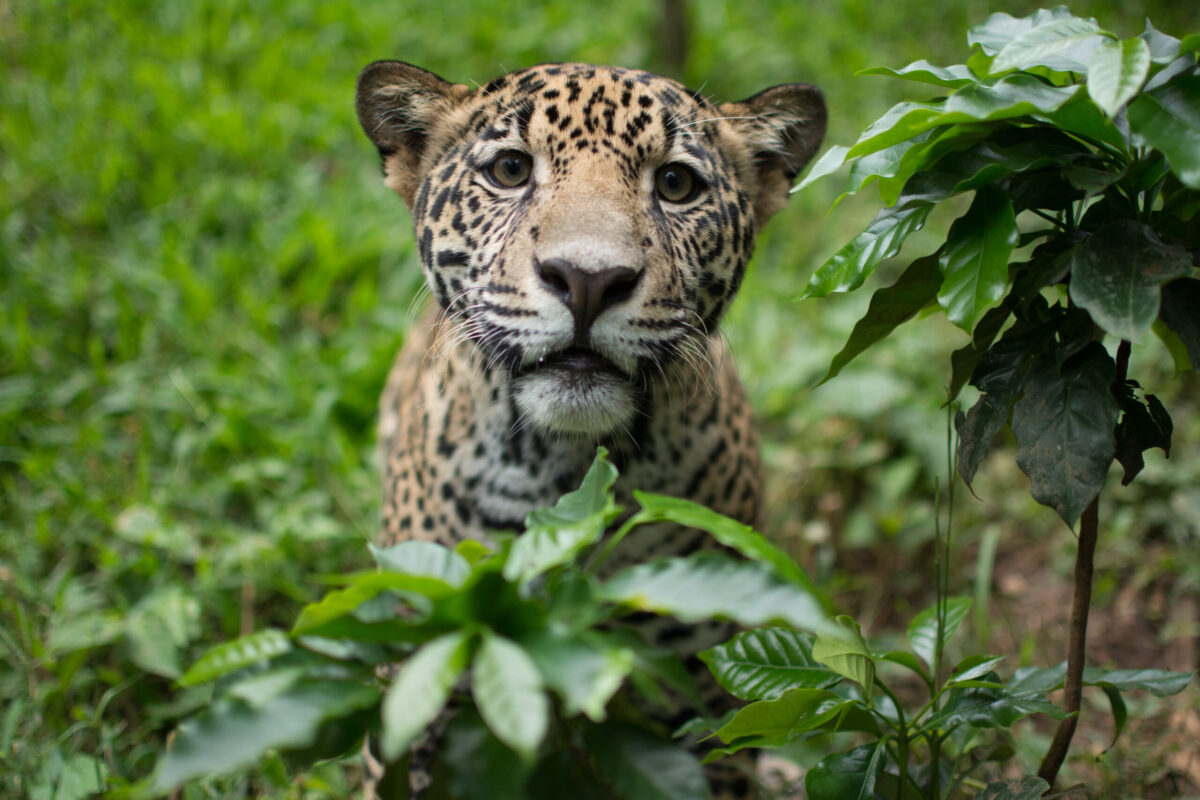
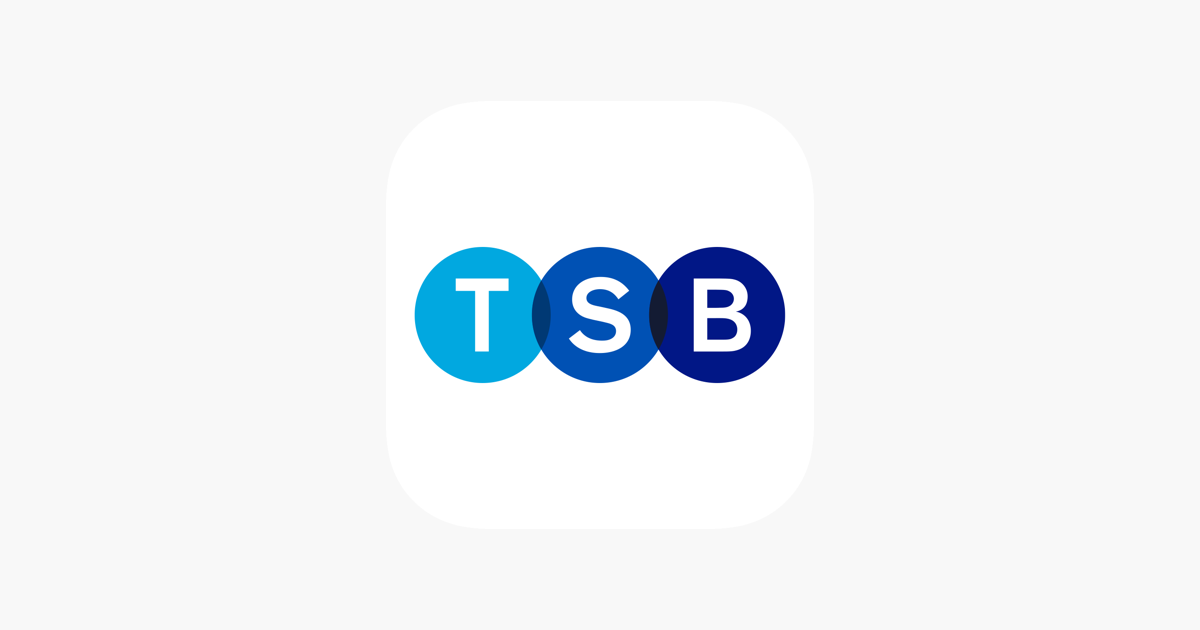

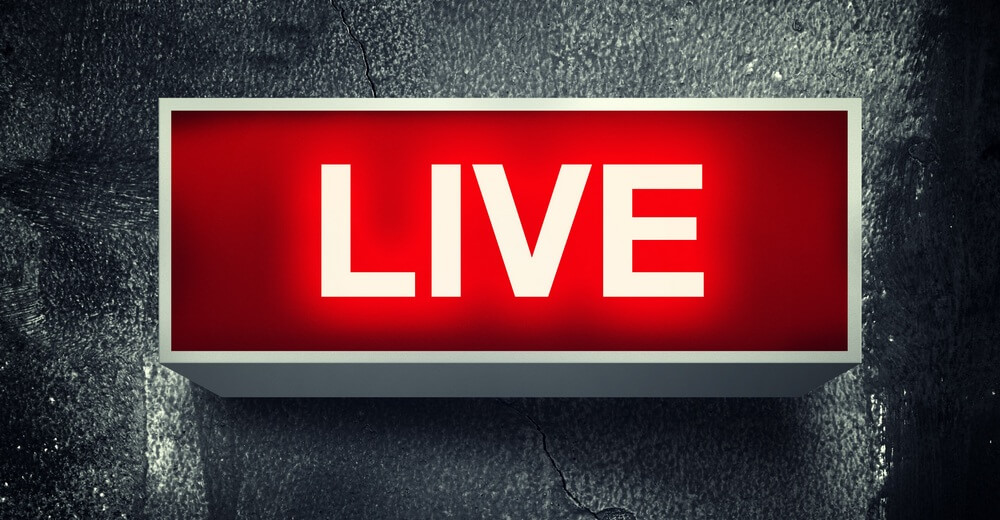
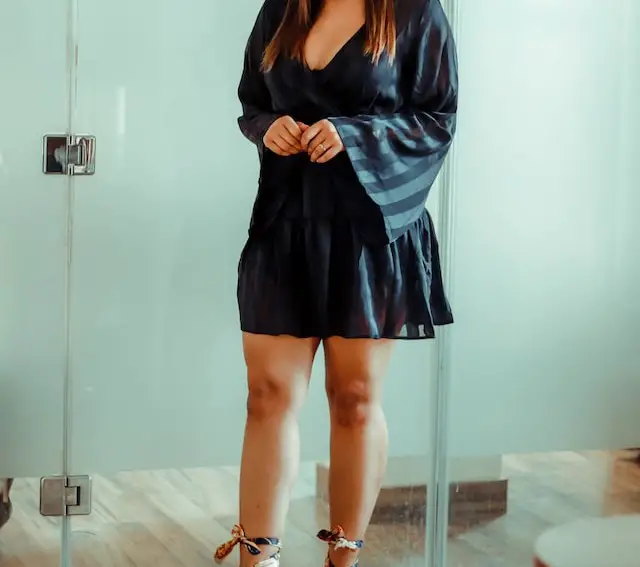
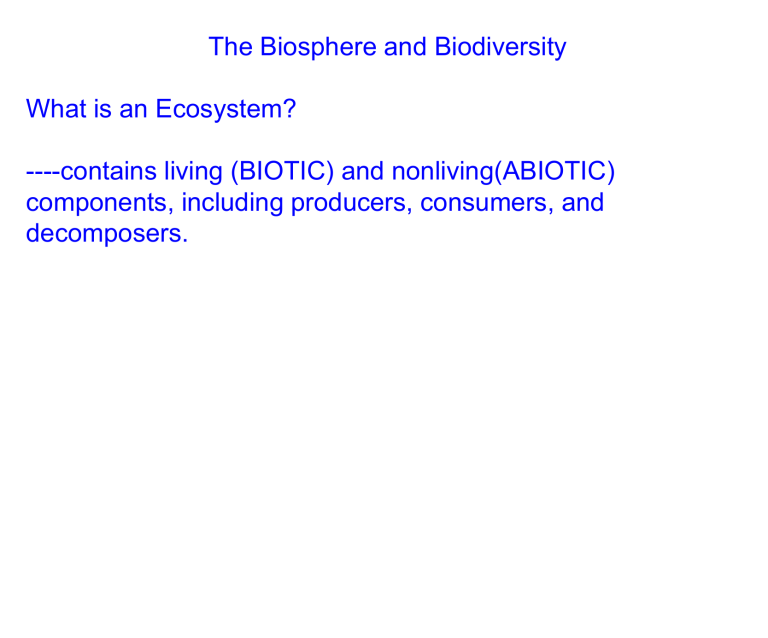
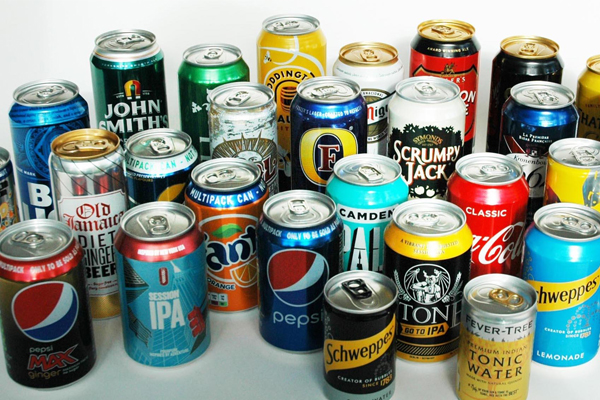
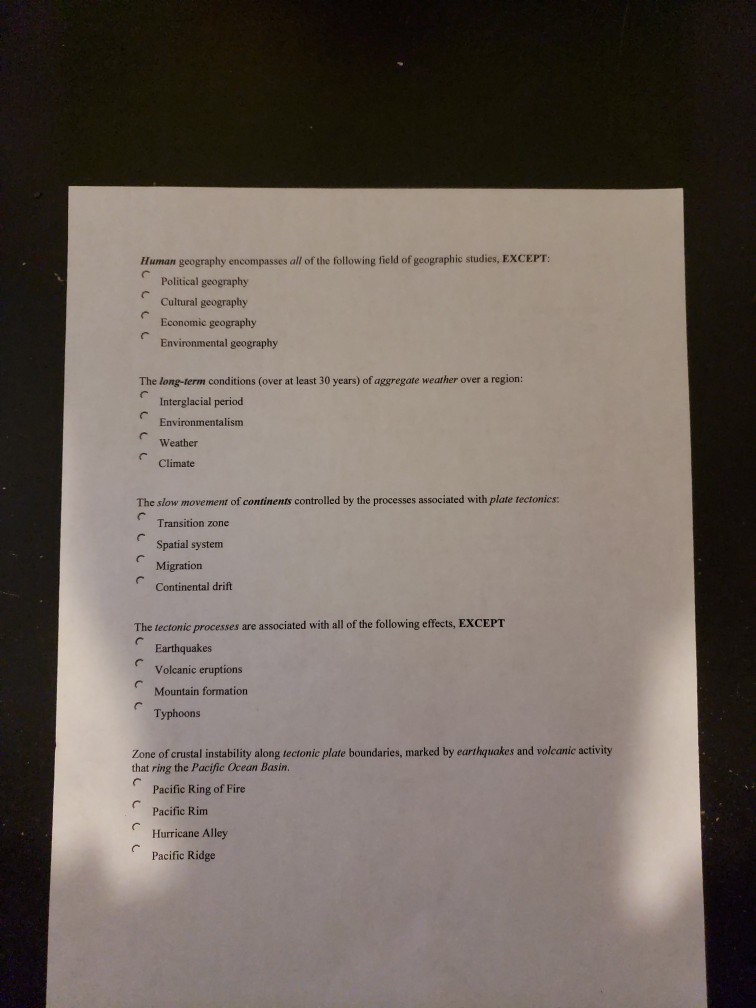

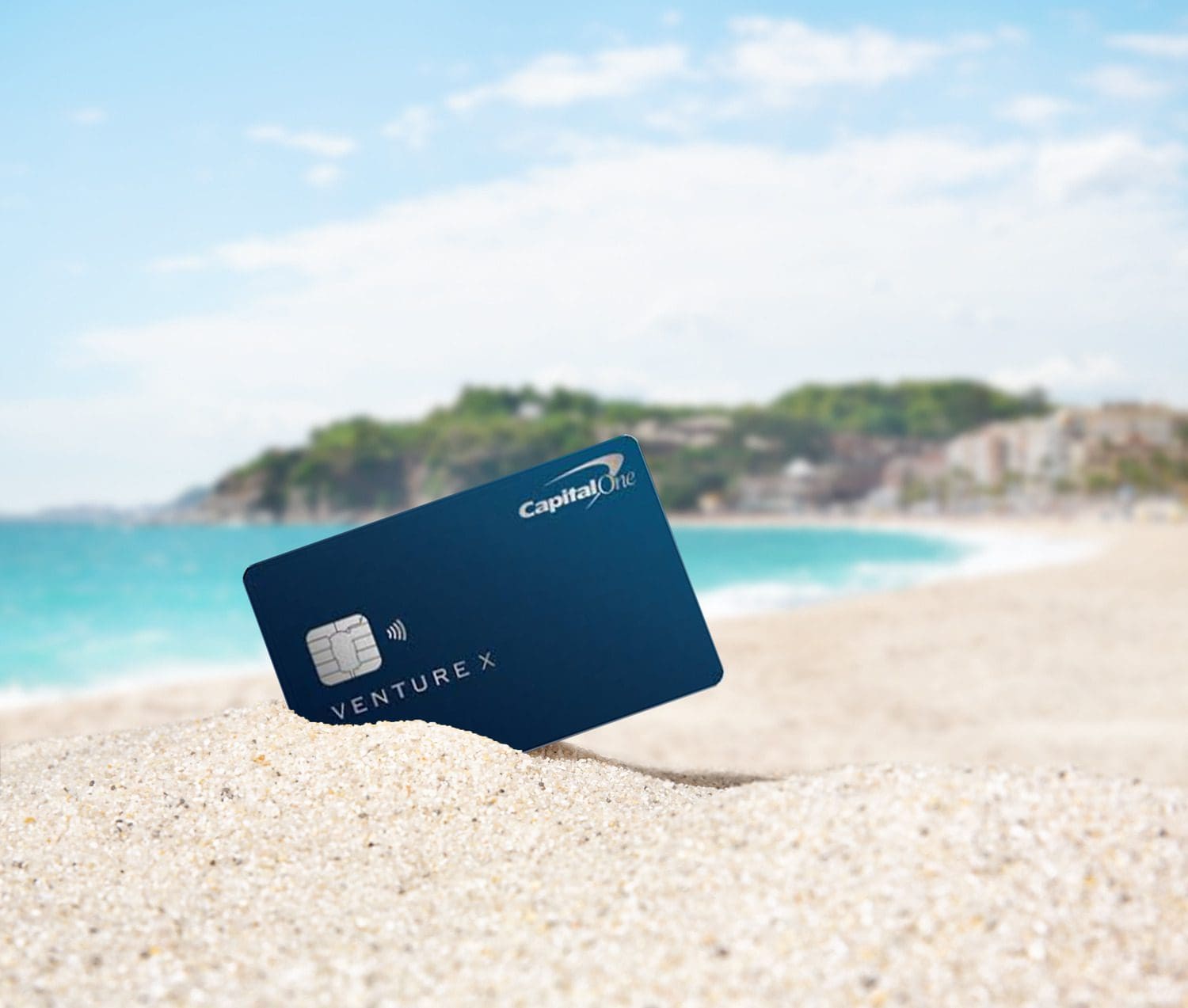