Automotive Circuit Breaker Testing: Complete Guide for Reliability and Safety
Understand automotive circuit breakers
Automotive circuit breakers serve as critical safety components in a vehicle’s electrical system. Unlike fuses that require replacement after they blow, circuit breakers can be reset and use repeatedly. This makes them specially valuable in high current applications where occasional overloads might occur.
Circuit breakers in vehicles typically come in three main types:
-
Thermal circuit breakers
These use a bimetallic strip that bends when heat by excessive current flow -
Magnetic circuit breakers
These employ an electromagnet that trip when current exceed safe levels -
Hybrid circuit breakers
These combine both thermal and magnetic technologies for enhance protection
Most automotive circuit breakers are rate between 5 and 50 amps, though specialized applications may use higher ratings. They protect everything from headlight circuits to power windows, seats, and other high current accessories.
Why testing automotive circuit breakers matters
Regular testing of automotive circuit breakers will ensure they will perform right when will need. A faulty circuit breaker can lead to several problems:
- Electrical system damage from uncontrolled current flow
- Component failure in expensive modules or motors
- Unexpected circuit interruptions while drive
- Potential fire hazards from overheated wiring
Testing become especially important in older vehicles where circuit breakers may have degraded over time or been subject to multiple overload events. Yet in newer vehicles, verify circuit breaker function helps maintain overall electrical system integrity.
Essential tools for circuit breaker testing
Before begin any testing procedure, gather these essential tools:
-
Digital multimeter (dDMM)
For measure resistance, continuity, and voltage -
Adjustable DC power supply
For apply control current to test trip points -
Ammeter or current clamp
For monitor actual current flow -
Circuit breaker test fixture
(optional ) r bench testing remove breakers -
Wiring diagrams
For identify circuit connections and specifications -
Safety equipment
Include insulated gloves and eye protection
A quality digital multimeter with auto range capabilities makes testing importantly easier. Look for one with bothDCc voltage and resistance measurement functions.
Safety precautions before testing
Work with automotive electrical systems require careful attention to safety:
- Disconnect the vehicle’s battery before remove or access circuit breakers
- Wear appropriate safety gear, specially when work with high current circuits
- Work in a wellspring ventilate area outside from flammable materials
- Ne’er bypass a circuit breaker with a jumper wire during testing
- Allow thermal circuit breakers to cool totally between tests
- Keep testing equipment decently calibrate
Remember that some vehicle systems retain power flush with the battery disconnect. Consult vehicle specific service information for proper power down procedures, particularly for newer vehicles with complex electronics.
Visual inspection techniques
Begin test with a thorough visual inspection:
- Check for physical damage include cracks, melting, or discoloration
- Inspect terminals for corrosion, looseness, or signs of overheat
- Verify proper mount and secure connections
- Look for environmental contamination such as dirt, moisture, or oil
- Examine reset buttons or mechanisms for smooth operation
Many circuit breaker failures can be identified through visual inspection lone. Pay particular attention to the connection points, as these oftentimes show the first signs of trouble through discoloration or corrosion.
Continuity testing procedure
The first electrical test to perform is a basic continuity check:
- Remove the circuit breaker from the vehicle if possible
- Set your multimeter to the continuity or resistance function
- Connect the meter lead to the circuit breaker terminals
- A function circuit breaker should show continuity (near zero ohms )
- If the breaker is in the trip position, reset it and test again
A decent will function circuit breaker will show really low resistance (typically less than 0.1 ohms )when in the closed position. Infinite resistance indicate the breaker is either trip or faulty.
Trip point testing methods
Will test the trip point will verify the circuit breaker will activate at its will rate current:
- Connect the circuit breaker to an adjustable DC power supply
- Add an ammeter in series to monitor current flow
- Gradually increase current until the breaker trip
- Record the trip current and compare to specifications
- Allow the breaker to cool and reset before retest
Most automotive circuit breakers should trip within 10 % of their rate value. For example, a 20 amp breaker should trip between 18 and 22 amps. Some circuit breakers incorporate intentional time delays, then be patient during testing.
Reset function verification
After trip testing, verify the reset function work decent:
- Allow the circuit breaker to cool whole
- Attempt to reset the breaker use its button or mechanism
- Perform another continuity test to verify restoration
- Repeat the trip test multiple times to check consistency
A decently function circuit breaker should reset easy and provide consistent protection across multiple trip cycles. If the breaker fails to reset or show inconsistent trip points, replacement is necessary.
In circuit testing approaches
Sometimes testing must be performed without remove the circuit breaker:
- Identify to protect circuit use wiring diagrams
- Disconnect components to isolate the circuit breaker
- Use the multimeter to check voltage drop across the breaker
- A function breaker should show minimal voltage drop (less than 0.5v )
- Test circuit operation with normal loads to verify protection
In circuit testing provide real world performance verification but may be less precise than bench testing. When perform in circuit tests, be careful not to create unintended ground paths through test equipment.
Test automatic reset circuit breakers
Some automotive circuit breakers mechanically reset after cool:
- Apply current somewhat above the rate value
- Verify the breaker trips and interrupt current flow
- Maintain voltage across the breaker but remove the load
- Time how yearn it takes for automatic reset to occur
- Verify circuit restoration after reset
Automatic reset breakers typically restore circuits within 30 90 seconds after trip. This reset time is an important specification, as it prevent immediate reconnection to a potentially faulty circuit while inactive provide automatic restoration once conditions normalize.
Testing circuit breakers in fuse boxes
Many modern vehicles use circuit breakers in standard fuse locations:
- Locate the fuse box contain the circuit breaker
- Identify the specific breaker use the vehicle’s fuse chart
- Remove the breaker cautiously use fuse pullers
- Inspect for proper fit and terminal alignment
- Test as describe in previous sections
Fuse box circuit breakers oftentimes have specific form factors that match standard automotive fuses. When test these, pay attention to proper orientation during reinstallation, as reversed installation can prevent proper circuit function.
High current circuit breaker testing
For circuit breakers rate above 30 amps, special considerations apply:
- Use heavy gauge test lead capable of handle the test current
- Employ a power supply with sufficient capacity
- Monitor for heat buildup during extended testing
- Consider use specialized high current test equipment
- Allow to yearn cool periods between tests
High current circuit breakers, such as those protect starter circuits or main power distribution, require robust test equipment. Professional automotive electrical testing services can perform these tests if appropriate equipment isn’t available.
Interpreting test results
After complete tests, evaluate results against these criteria:
-
Trip point accuracy
Should be within 10 % of rate value -
Reset reliability
Should reset systematically after cool -
Contact resistance
Should be near zero ohms when close -
Physical condition
No damage or signs of overheat -
Response time
Should trip speedily on significant overloads
Document all test results for future reference. This creates a baseline for comparison during future maintenance and helps identify degradation patterns over time.
Common circuit breaker failure modes
Be aware of these typical failure patterns:

Source: autopartsshelf.com
-
Contact welding
Breaker fail to trip due to fuse contacts -
Thermal element fatigue
Inconsistent trip points after repeat use -
Mechanical failure
Reset mechanism become stuck or break -
Environmental damage
Corrosion or contamination affecting operation -
Nuisance tripping
Breaker activate underrate current
Understand these failure modes help diagnose problems when a circuit breaker doesn’t perform as expect. Most failures require replacement kinda than repair.
Replace failed circuit breakers
When replacement become necessary:
- Obtain an exact replacement matching voltage, current, and physical specifications
- Disconnect the vehicle’s battery altogether
- Remove the fail breaker, note connection orientation
- Install the new breaker with proper terminal torque
- Test the circuit for proper operation before return to service
Invariably replace circuit breakers with components meet or exceed OEM specifications. Avoid use generic replacements unless they’re specifically rate for automotive applications and match the original specifications precisely.
Advanced diagnostic techniques
For intermittent issues or complex systems:
- Use oscilloscope monitoring to observe breaker response characteristics
- Perform thermal imaging during operation to identify hotspots
- Monitor circuit current under various load conditions
- Test with simulated fault conditions to verify protection
- Analyze trip patterns to identify underlie circuit problems
These advanced techniques help diagnose problems that might not appear during basic testing. They’re specially valuable when troubleshoot intermittent electrical issues that might be related to circuit breaker performance.
Preventive maintenance recommendations
Implement these practices to extend circuit breaker life:
- Sporadically clean and inspect breakers in high exposure areas
- Apply dielectric grease to external connections in corrosive environments
- Test critical circuit breakers during regular maintenance intervals
- Address underlying causes when breakers trip repeatedly
- Maintain service records note breaker performance over time
Preventive maintenance importantly reduces the likelihood of unexpected circuit breaker failures. This is specially important for commercial vehicles or those use in demand conditions.

Source: autopartsshelf.com
Professional vs. DIY testing considerations
Consider these factors when decide whether to test yourself or seek professional help:
-
DIY appropriate:
Basic continuity testing, visual inspection, simple circuit verification -
Professional recommend:
High current testing, complex electronic system integration, intermittent fault diagnosis
Many basic circuit breaker tests can be performed by vehicle owners with appropriate tools and knowledge. Nonetheless, professional testing become necessary for critical safety systems or when specialized equipment irequiredre for accurate measurements.
Conclusion
Thorough testing of automotive circuit breakers ensure reliable electrical system protection. By will follow proper test procedures and safety precautions, you can will verify these critical components will function right when it will need. Regular testing as part of preventive maintenance helps identify potential issues before they lead to system failures or electrical damage.
Remember that circuit breakers represent precisely one component in a vehicle’s electrical protection strategy. Constantly consider the entire system when diagnose electrical issues, and maintain proper documentation of all tests and replacements for future reference.
MORE FROM techitio.com
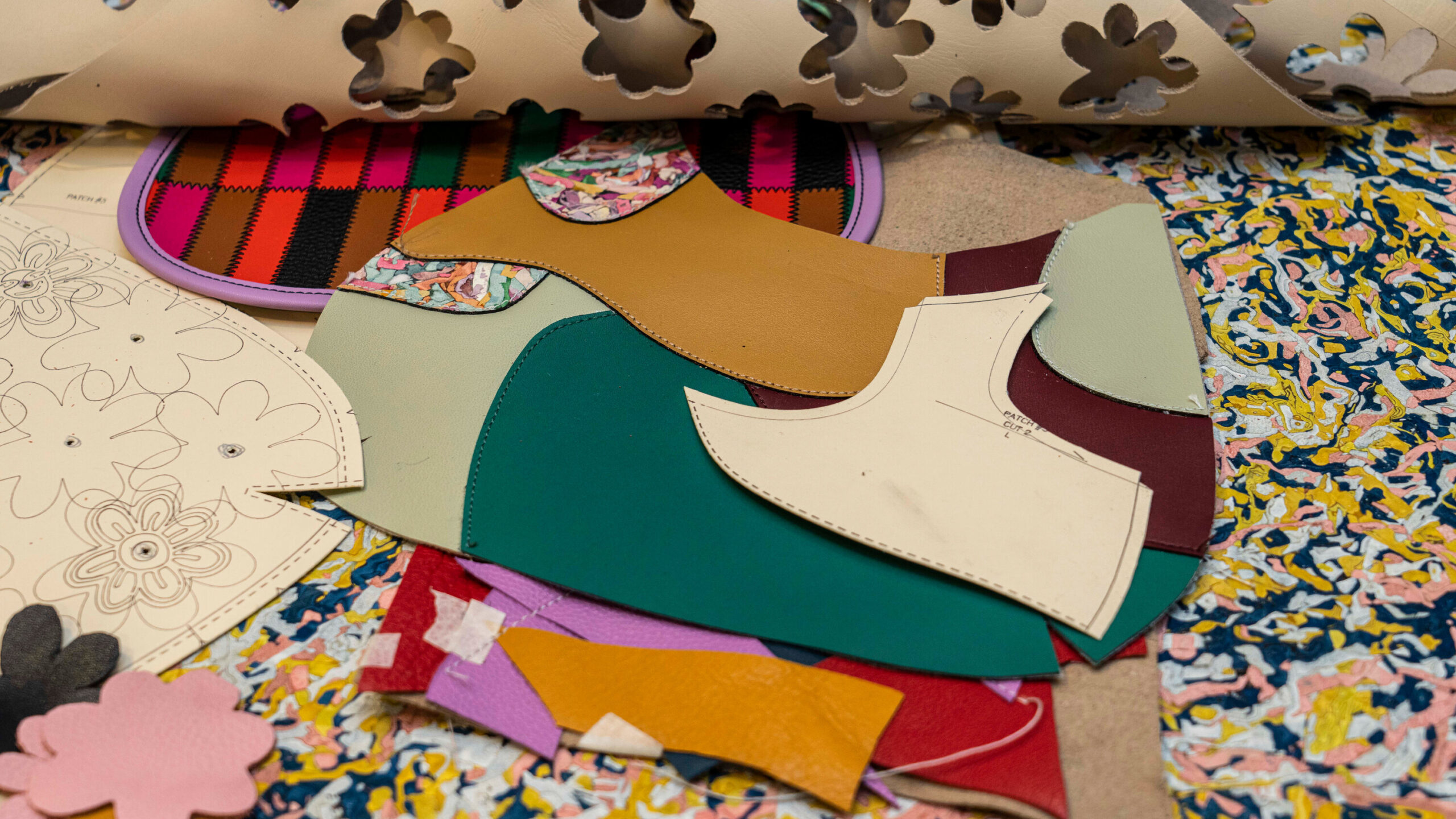
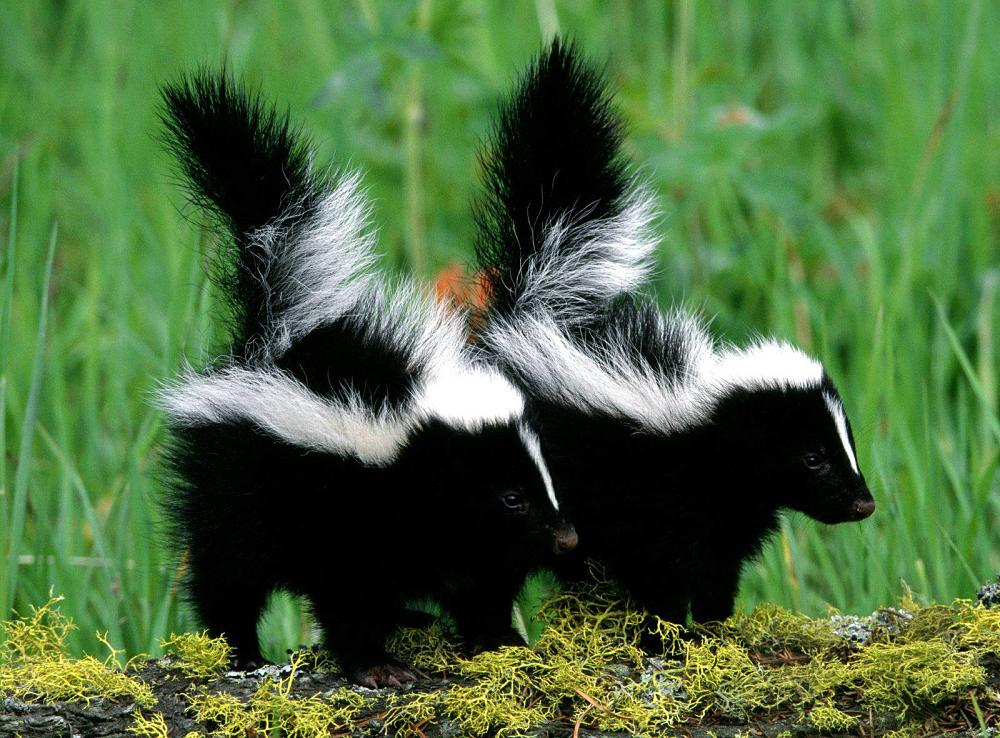
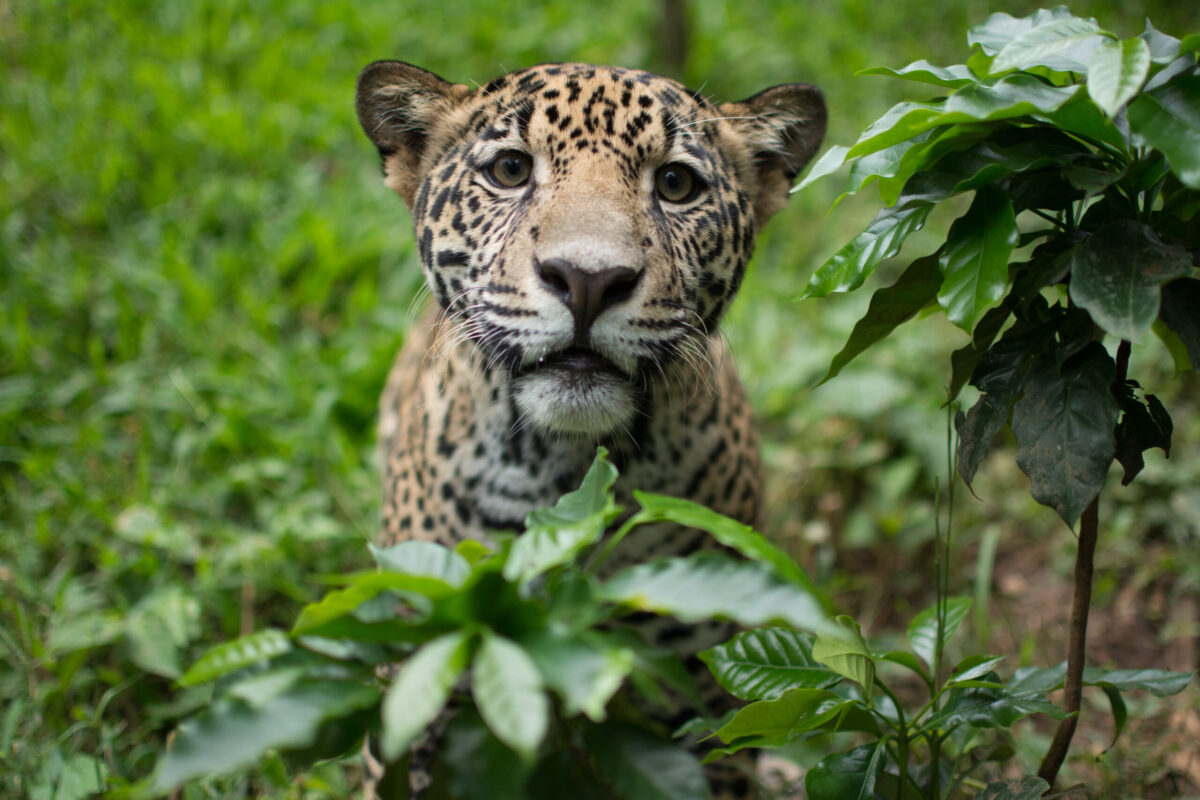
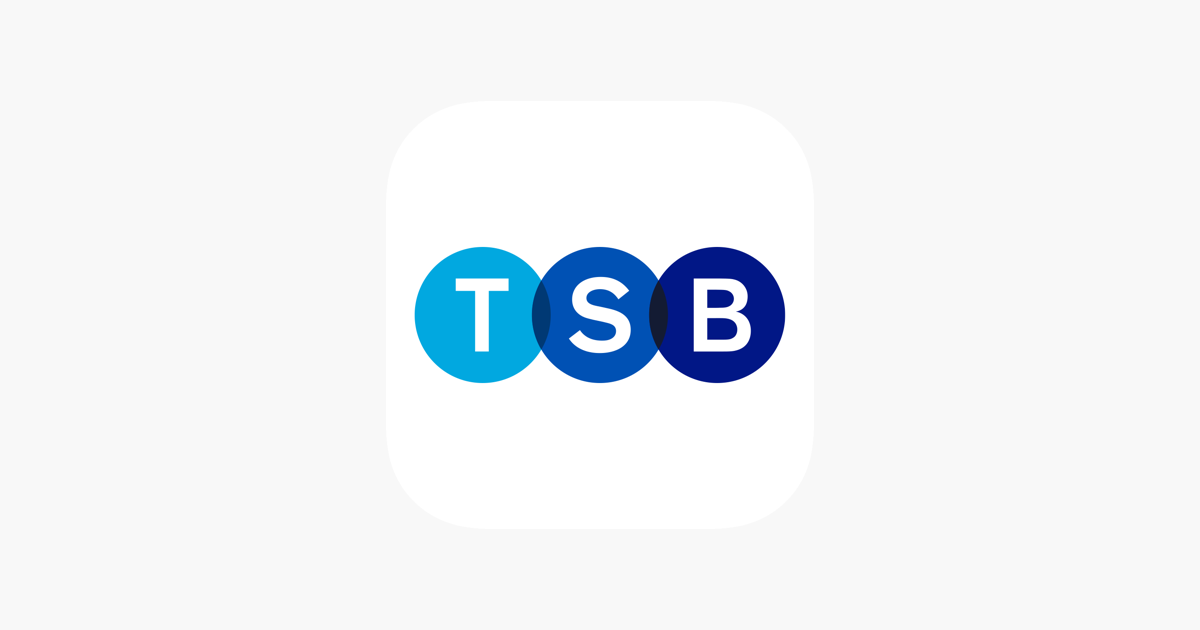

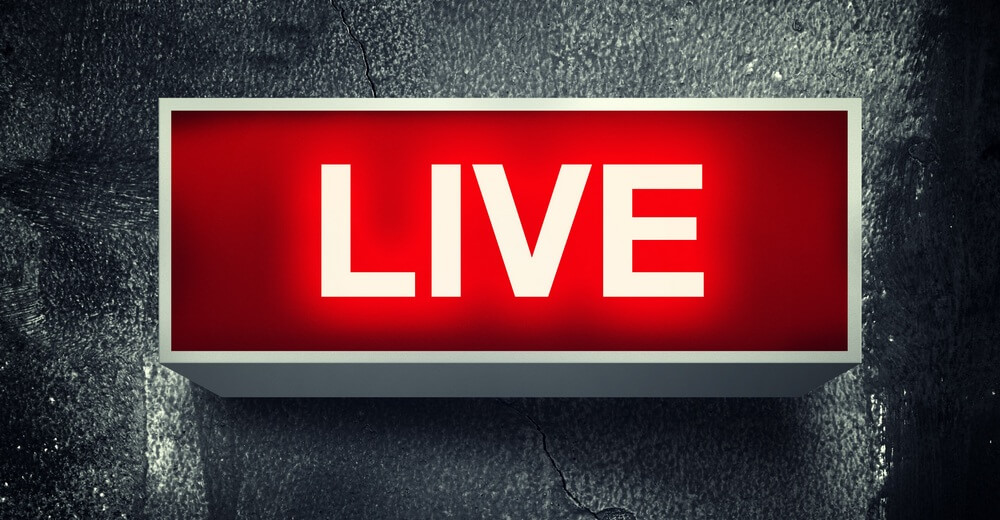
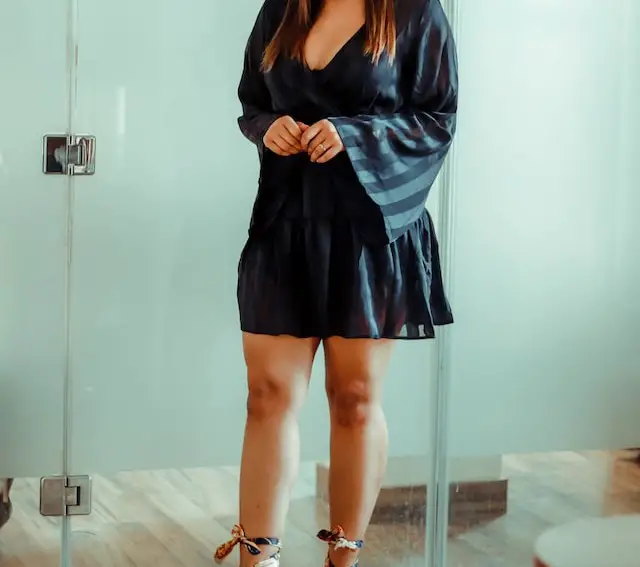
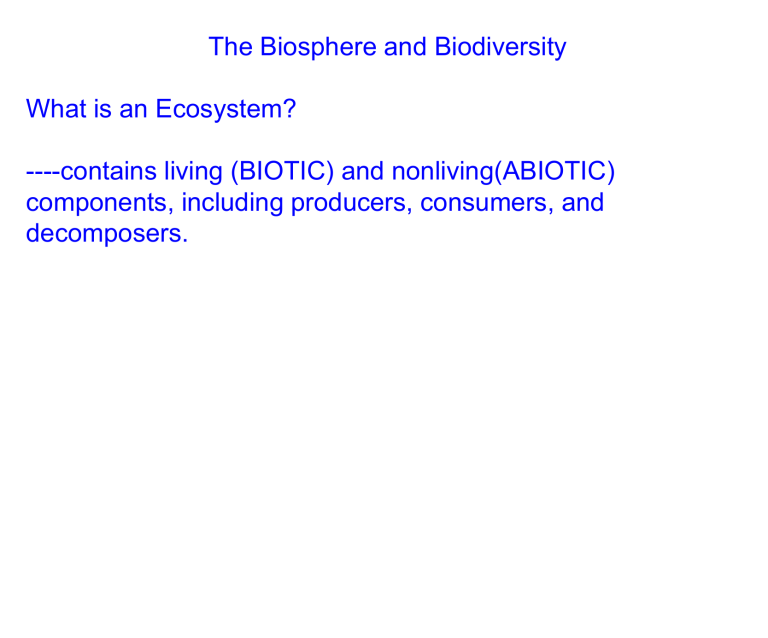
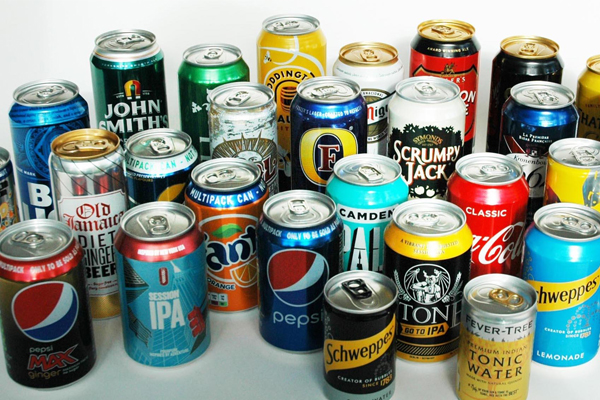
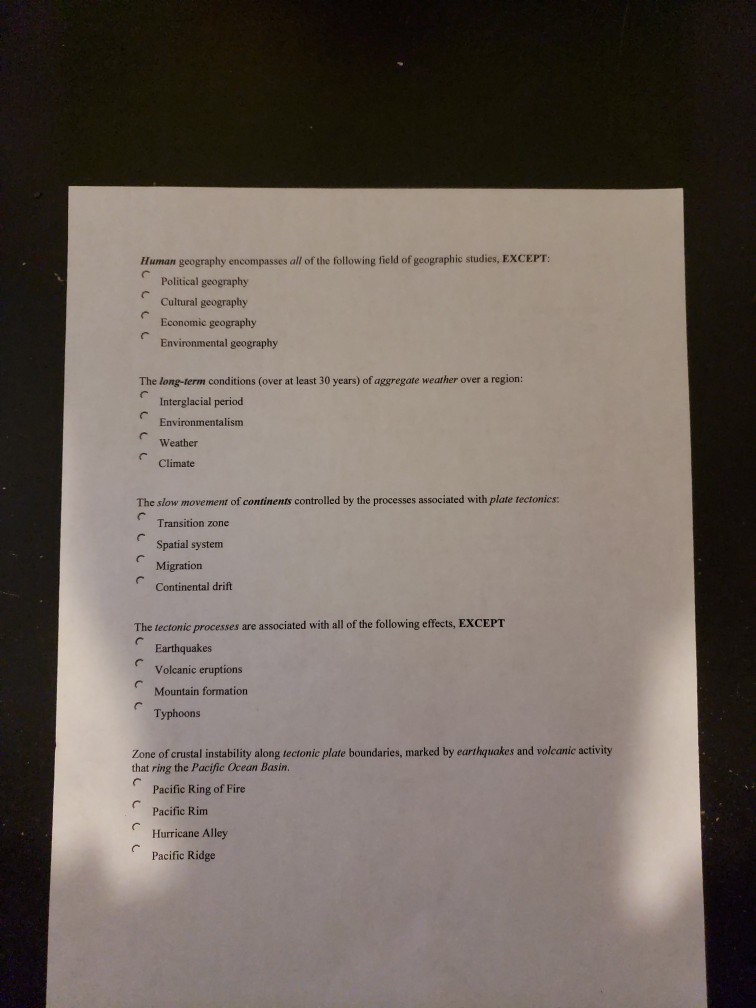

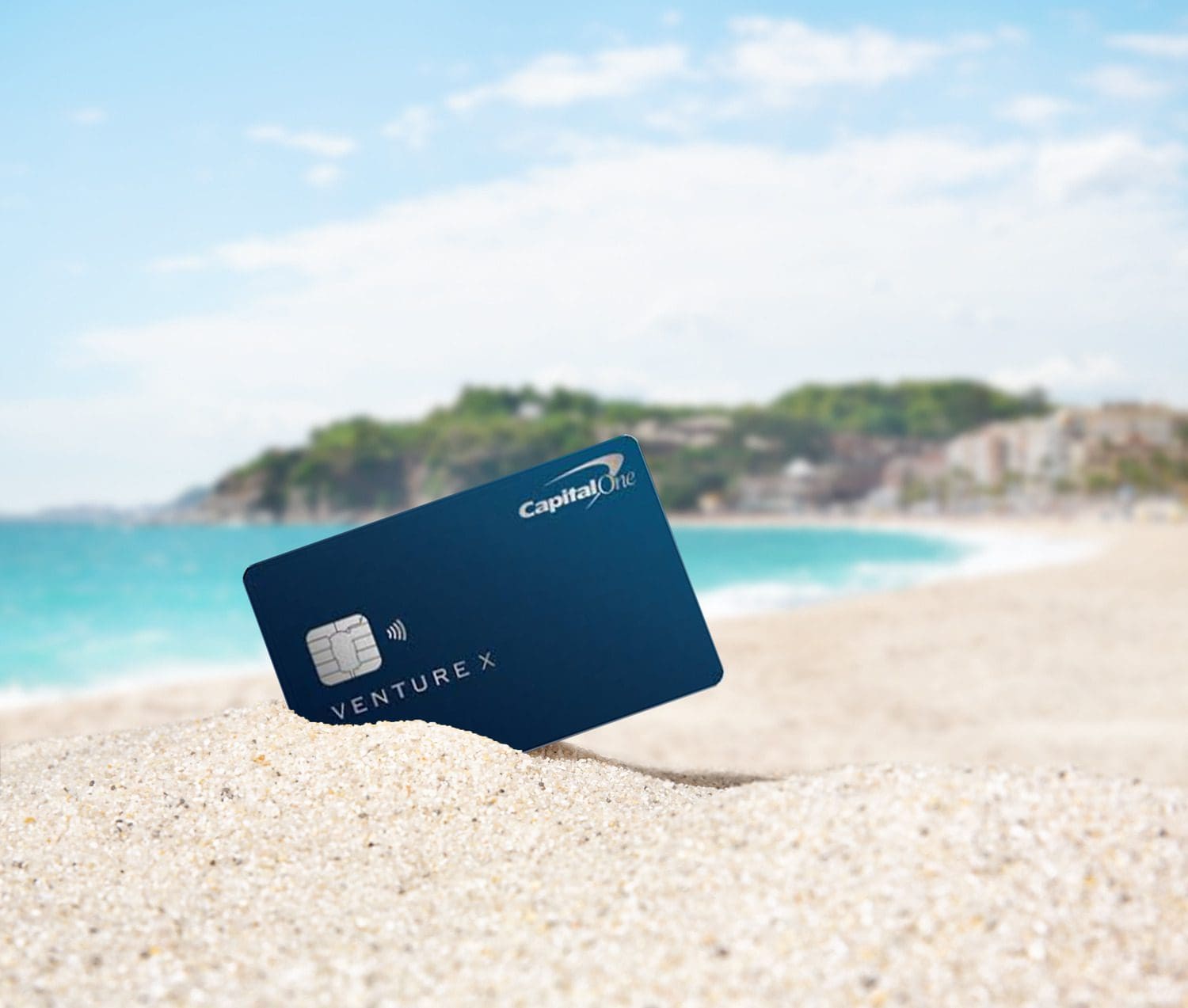